Fulton Bellows Introduces Revolutionary Hydrogen Furnace
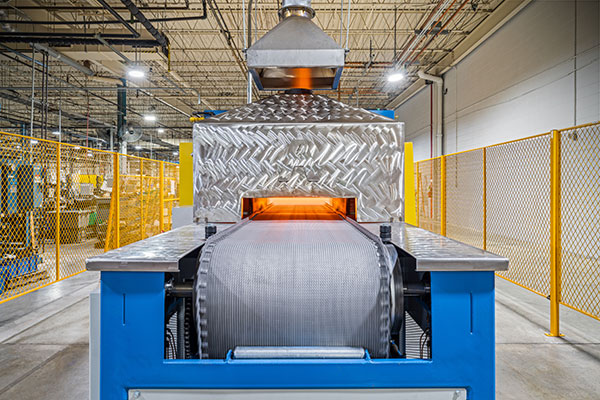
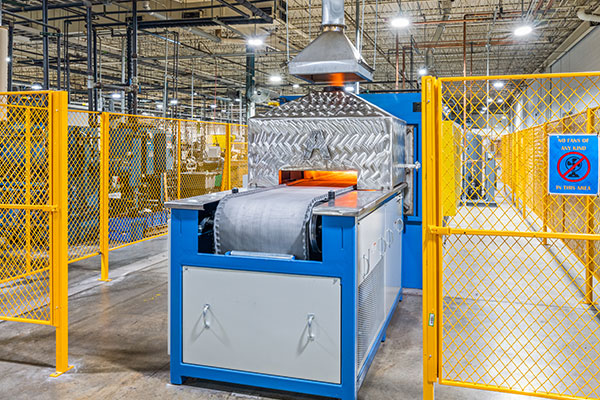
Fulton Bellows has unveiled an innovative hydrogen furnace, signaling a significant advancement in metallurgical processes, particularly in annealing applications.
This cutting-edge furnace is poised to transform the treatment of both ferrous and nonferrous alloys, providing enhanced control over time and temperature relations to achieve superior properties.
The key breakthrough of the hydrogen furnace lies in its use of a hydrogen atmosphere during annealing. Not only is it vastly more Eco friendly, this progressive method, involves saturating metal surfaces with hydrogen, displacing atmospheric oxygen that typically leads to undesirable oxides. In contrast to traditional vacuum furnaces that remove oxygen, Fulton Bellows’ hydrogen furnace excels in pulling oxides out of the stainless surfaces and greatly enhancing the prevention of oxide infusion during any anneal cycle. These enhanced processes also aid in promoting superior surface conditions.
The modern design of the hydrogen furnace is a notable advantage, marking a departure from the decades-old infrastructure of existing furnaces. The continuous belt driven process not only enhances quality, it significantly, helps reduce lead times.
While older furnaces continue to play a crucial role in the manufacturing process for Inconels, the introduction of the hydrogen furnace, will focus on brass, bronze, stainless steel, and Monel alloys; Supporting Fulton Bellows’ commitment to adopting state-of-the-art technology for improved efficiency and reliability.
Furthermore, the hydrogen furnace introduces an innovative approach to consistency. Unlike traditional vacuum furnaces where parts are stacked in baskets, the hydrogen furnace utilizes a continuous belt, ensuring each part passes through heated zones individually. This design enhances consistent heating, resulting in superior tubes and contributing to the production of higher-quality bellows.
Fulton Bellows’ hydrogen furnace marks a remarkable leap forward in annealing technology, offering precise control, improved surface conditions, and enhanced part-to-part consistency. It underscores the company’s commitment to advancing metallurgical processes.